August 31, 2023
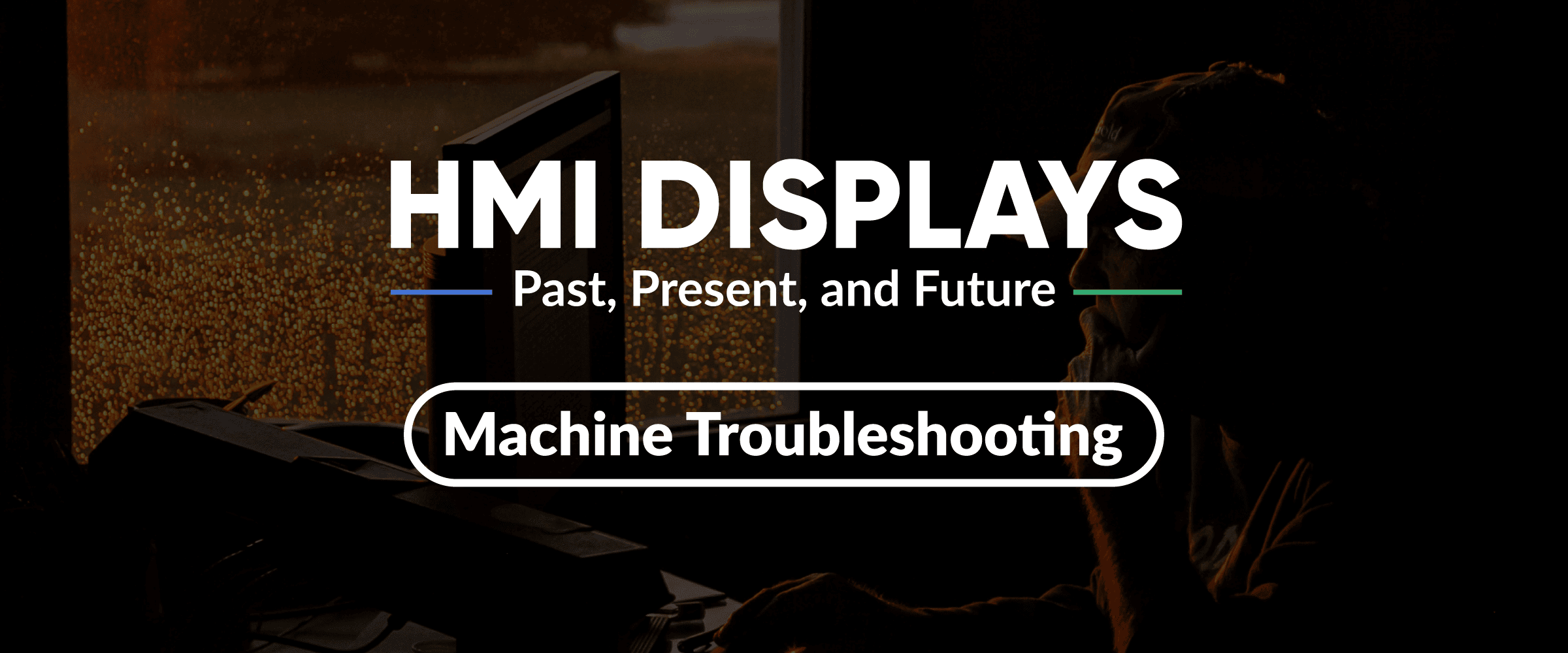
In the evolving landscape of mobile machinery used in industries like agriculture, construction, oil and gas, and mining, the role of Human-Machine Interface (HMI) displays has been pivotal. These displays are not merely screens; they act as the operator’s primary touchpoint for machine interaction and troubleshooting. Let’s embark on a journey through the past, present, and future of troubleshooting through HMI displays.
Then: Simple Warnings
Simple Warnings and Alerts
In the past, HMI displays utilized basic signal methods like flashing lights or auditory buzzers to warn operators. For instance, a light might flash red to indicate low fuel or an alarm might sound for engine overheating. The focus was purely on alerting the operator that a particular component needed attention. There was no accompanying diagnostic data or guidance on how to remedy the issue.Why was this limited?
Technological Limitations
Around 10-20 years ago, HMI displays were constrained by the then-available technology. Limited processing capabilities meant they could only manage rudimentary tasks like displaying basic alerts.Cost Constraints
Advanced troubleshooting features were not only complicated to integrate but also prohibitively expensive, deterring manufacturers from offering more than basic functionalities.Lack of Sensory Inputs
The machines themselves often lacked advanced sensors, leaving HMI displays with minimal information to relay for troubleshooting purposes.Examples Then
Agricultural Equipment
Older models of tractors and harvesters relied heavily on a series of lights and audible alarms. These would signal rudimentary statuses like fuel level, engine overheating, or battery status.Construction Machinery
Equipment like bulldozers and backhoes usually came with basic HMI displays, which often included a series of lights or a monochromatic text display that might flash ‘Engine Failure’ or ‘Hydraulic System Error.’Oil and Gas Equipment
Old drilling equipment had minimalistic HMI displays that used alphanumeric characters to spell out issues like ‘Drill Fail’ or ‘Pressure High’ without offering any solutions.Now: Advanced Warnings and Diagnostics
Detailed Warnings
Unlike simple alerts, detailed warnings offer a comprehensive view of what’s going wrong. For example, instead of a generic “Engine Failure” alert, the HMI may specify that there’s a “Coolant Level Low: Risk of Engine Overheat.”Diagnostics Options
Modern HMI displays offer a suite of diagnostic tools that allow the operator or maintenance personnel to probe deeper into the problem. For instance, if an “Oil Pressure Low” warning is displayed, the HMI may allow the user to view pressure graphs, history logs, or even run a quick diagnostic check.Predictive Maintenance
Leveraging real-time data from various sensors, today’s onboard systems can predict when a specific machine part is likely to fail, allowing for preventative action. For example, a sensor monitoring vibration may feed data to the controller or the cloud, which then calculates wear and tear, subsequently alerting the operator via the HMI to perform maintenance before a failure occurs.How is this possible?
Technological Advancements
With advancements in HMI and controller processing speed and cloud connectivity options, – modern HMIs can give operators access to complicated diagnostics information and display it in an intuitive way.Increased Sensor Integration
Mobile machinery now boasts an array of sensors that continuously monitor various components, providing a rich dataset that HMI displays can use for analytics and troubleshooting.Examples Today
Oil and Gas Equipment
Current drilling rigs offer sophisticated HMI displays that not only flag issues but can also run a diagnostic check, suggesting probable causes and even potential solutions.Agricultural Machinery
Tractors and combines now offer predictive maintenance alerts through their HMI displays, advising operators to replace or service parts like air filters or hydraulic systems before they fail, thus reducing downtime.Construction Equipment
Modern cranes have HMI displays capable of detailing issues like ‘Wire Friction High’ and advising operators to either slow down the operation or lubricate the wires.What Might be Next in Machine Troubleshooting
Self-Diagnosing
As technology advances, HMI displays are likely to become capable of diagnosing issues on their own without any human intervention. They might automatically run a series of tests upon detecting an anomaly and determine the root cause.Advanced Predictive Maintenance
Future HMIs are expected to utilize sophisticated algorithms to analyze more variables, such as weather conditions, machine usage patterns, and industry trends, to offer even more precise and timely maintenance predictions.Automated Fixes
This would be the pinnacle of HMI troubleshooting technology, where the machine would not only diagnose its own issues but also correct them either without human input or by providing the operator with the option to initiate automated fixes.How could this be possible?
Machine Learning & AI
As we look to the future, machine learning and artificial intelligence are poised to make HMI displays even smarter. The machines themselves will be capable of self-diagnosing issues, perhaps even before they become critical.MM-IoT Connectivity
Mobile Machine Internet of Things (MM-IoT) technology is only getting better and enables machinery to be interconnected. By sharing data and insights through the use of next-generation wireless networks and higher processing capabilities this could allow for collective troubleshooting and quicker fixes.User Expectations
As consumer technology advances, the expectation for industrial machinery to be just as intelligent will grow, pushing the need for advanced troubleshooting features.Examples Tomorrow
Automated Fixes in Mining Equipment
In a future where a mining drill’s HMI detects a failing drill bit, it could not only alert the operator but also autonomously contact a connected inventory system to order a replacement part. It could then guide the operator through the replacement process via augmented reality.Advanced Predictive Maintenance in Agricultural Machinery
Tractors of the future could employ machine learning to analyze historical data on crop yields, soil conditions, and equipment usage to predict when key components are likely to fail, thus offering timely maintenance alerts.Self-Diagnosing in Construction Machinery
Cranes might soon be equipped with HMIs that, upon detecting a malfunction, automatically run a series of diagnostic tests, then either initiate an automatic fix or provide the operator with a series of options for manual intervention.Conclusion
Mobile hardware technology and HMI displays have come a long way in their capability to assist with troubleshooting issues in mobile machinery. From simple alert systems to sophisticated predictive maintenance protocols, they continue to evolve. The future promises HMI systems with even more autonomy and intelligence, shaping a new era of efficiency and reliability in mobile machinery.Looking for displays?
Learn more about our inSIGHT displays and make the next-generation upgrade on your mobile machines – today.
Explore More
About STW Technic
STW Technic is an innovative leader in the design, manufacture, and implementation of electronic solutions for mobile machines and off-highway vehicles. We partner with machine manufacturers, system integrators, and distributors to provide engineered and highly reliable connectivity, automation, and power management solutions to truly empower their mobile machines. We offer the latest in Mobile Machine IoT hardware and software solutions, such as our market-leading remote asset management platform – Reach. We also provide solutions such as openSYDE – our systems configuration tool – to support the entire lifecycle of your machine.