August 25, 2023
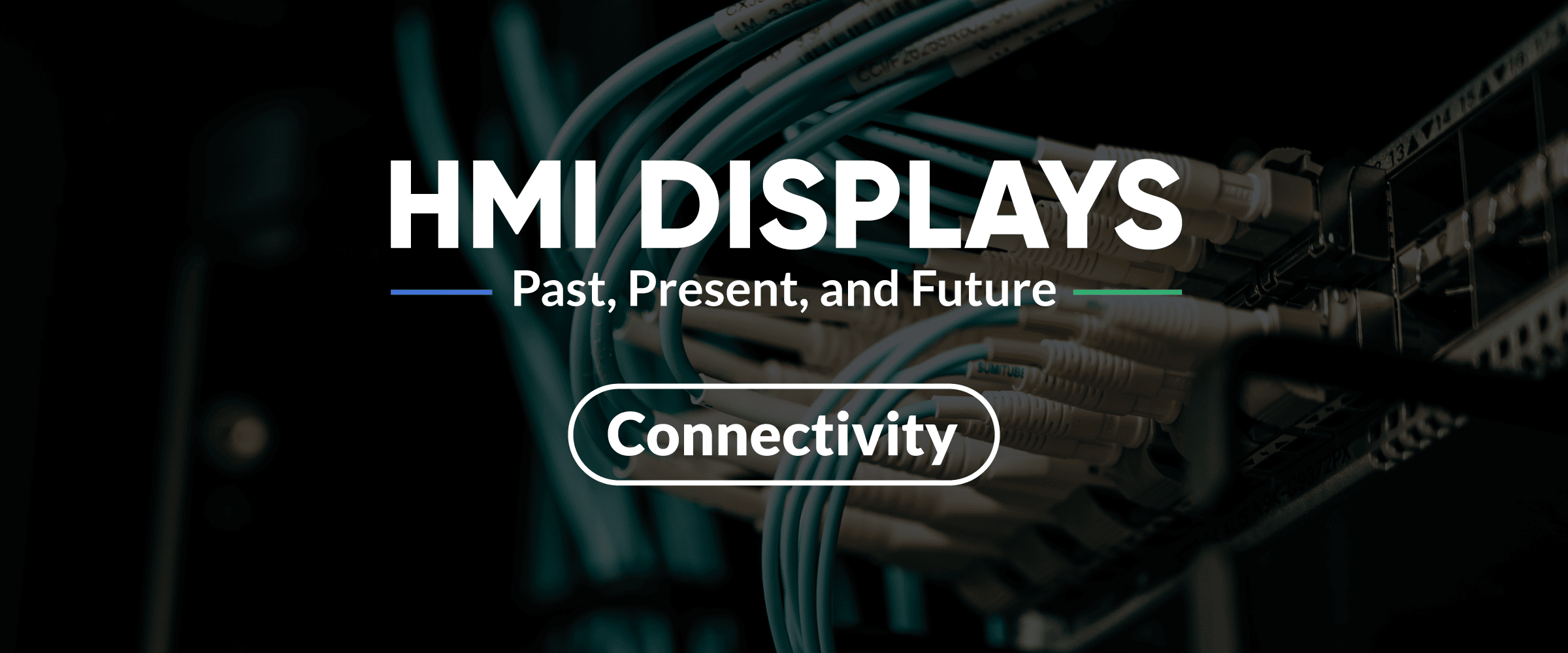
Then: A Look at Earlier Protocols
Serial RS232
Serial RS232 was a key protocol in the past, enabling basic communication between devices. Its simplicity, widespread availability, and lower cost made it an attractive option for various industries. Being non-networked, it was often used for point-to-point connections, allowing for direct and simple communication between two devices. Despite its lower data transmission speed, it was suitable for simpler control and monitoring applications where high-speed communication was not a priority.CAN-Bus
The Controller Area Network (CAN-Bus) has been fundamental in automotive and industrial applications. Its robust error-handling capabilities and ability to operate in noisy environments made it an essential tool for heavy equipment and machinery. Widely recognized for its real-time control and reliability, it allowed for decentralized and efficient communication between multiple devices. Its resilience to electrical interference and fail-safe mechanisms made it preferred in demanding settings like forestry and municipal vehicles.Ethernet (10/100 Mbit/s)
Early Ethernet protocols offered a balanced mix of speed and cost-effectiveness in connectivity. The Ethernet 10/100 Mbit/s became popular due to its compatibility with existing infrastructure and moderate data transfer rates suitable for the demands of the time. It provided a scalable solution with a capacity to handle an increasing number of connected devices. The flexibility and adaptability of the Ethernet protocol facilitated its integration into various industries, including marine and municipal services.Now: Modern Connection Protocols
CAN-Bus and CAN-FD
CAN-Bus has evolved to support more complex communication requirements. The introduction of CAN Flexible Data Rate (CAN-FD) enhanced CAN-Bus by allowing higher data rates, accommodating more data-intensive applications like advanced diagnostics. This evolution has particularly benefited electric and alternative fuel vehicles by enabling more sophisticated control systems. The extension of CAN-Bus with CAN-FD continues to offer robust and reliable connectivity, even as demands grow more complex.Ethernet (1 Gbit/s)
Today’s need for faster data transfer led to the evolution of Ethernet to support up to 1 Gbit/s speeds. This increase not only facilitates real-time data sharing and control but also enhances efficiency and performance in applications such as marine and forestry equipment. Its utilization in modern HMI displays has paved the way for more streamlined operations and data-driven decisions. The use of gigabit Ethernet continues to redefine connectivity standards, meeting the increasing requirements of today’s mobile machinery and heavy equipment.What Might be Next in Connectivity
Ethernet (>1 Gbit/s)
Why 1Gbit Ethernet is Likely the Next Generation The shift to Ethernet greater than 1000 Mbit/s, including 1Gbit Ethernet, is becoming increasingly apparent due to various compelling reasons: Data Intensity With the proliferation of big data, IoT, and real-time analytics, there is a growing need for faster data transmission, making 1Gbit Ethernet a logical step forward. Integration with Existing Technologies 1Gbit Ethernet can leverage existing Ethernet technologies, providing a scalable path that builds upon established protocols, which ensures easier integration and cost-effective implementation. Compatibility with Emerging Trends The growing trends in electric and alternative fuel vehicles, factory automation, and sophisticated machine learning algorithms require higher bandwidth, positioning 1Gbit Ethernet as an attractive solution. Faster Communication between Safety Systems High-speed Ethernet allows safety systems such as cameras and sensors to communicate and act faster than human operators, enabling immediate response to potential hazards. Enhanced Real-time Monitoring Increased data rates permit more detailed real-time monitoring, including thermal imaging and vibration analysis, leading to early detection of mechanical failures or abnormal conditions. Intelligent Coordination By connecting multiple safety systems, 1Gbit Ethernet facilitates coordinated actions, such as immediate shutdown of machinery if a fault is detected, minimizing risks to operators and equipment.Another Possibility: 5G Wireless
Enhanced Mobility With 5G, machinery equipped with HMI can communicate seamlessly across vast distances without relying on wired connections. This opens up new possibilities for remote operations and real-time control in mobile machinery, including marine, forestry, and municipal vehicles. Ultra-Low Latency 5G technology offers ultra-low latency, allowing near-instantaneous communication between devices. In safety systems, this enables immediate responses, such as activating emergency brakes or altering course if an obstacle is detected, potentially averting accidents. High Data Throughput The high data rates of 5G enable the transmission of large volumes of information, such as high-definition video feeds from cameras or complex sensor data. This allows for more comprehensive monitoring and control, enhancing both safety and efficiency. Robust Reliability 5G’s reliability ensures that critical communication channels remain stable even in challenging environments. In industries like marine or heavy equipment operation, where reliability is paramount, 5G could provide the robust connections needed. Integration with MM-IoT As Mobile Machine Internet of Things (MM-IoT) continues to expand, 5G’s ability to support a multitude of connected devices makes it a valuable asset for future HMIs. Whether managing a fleet of electric vehicles or overseeing a smart factory, 5G can facilitate interconnected operations that leverage the full potential of modern technology.Conclusion
As communication protocols evolve, so too do the capabilities of the machinery they support, driving innovation and efficiency in ways previously unimagined. The adoption of technologies like >1Gbit Ethernet and 5G wireless connectivity heralds a new era of innovation in the realm of HMI displays and mobile machinery. From enhancing machine safety to embracing integrated MM-IoT systems, the future of connectivity promises to transform the way we interact with and utilize heavy equipment across various industries.Looking for displays?
Learn more about our inSIGHT displays and make the next-generation upgrade on your mobile machines – today.
Explore More
About STW Technic
STW Technic is an innovative leader in the design, manufacture, and implementation of electronic solutions for mobile machines and off-highway vehicles. We partner with machine manufacturers, system integrators, and distributors to provide engineered and highly reliable connectivity, automation, and power management solutions to truly empower their mobile machines. We offer the latest in Mobile Machine IoT hardware and software solutions, such as our market-leading remote asset management platform – Reach. We also provide solutions such as openSYDE – our systems configuration tool – to support the entire lifecycle of your machine.